H2 Reallabor Burghausen
Motivation
In the joint project "H2 Reallabor Burghausen", the Chair of Energy Systems is working together with 37 partners from industry and science on the transformation of the chemical industry in the ChemDelta Bavaria towards a sustainable hydrogen-based circular economy. As a "lighthouse project", the project is intended to help achieve Germany's climate and energy policy goals and secure jobs and prosperity in the region. To make hydrogen useable as an energy source and material basis in the chemical industry, new technologies are being developed in seven different work packages and ideally brought to market maturity.
Aims
The Chair for Energy Systems is intensively involved in the overall coordination of the project as well as in simulation and experimental work on many of the funded work packages (WP):
AP1: System Aspects and Strategic Planning
Work package 1 focuses on energy system analysis to identify energy dependencies and synergies. Therefore, current and future potential, as well as the container concepts developed in the other work packages, are incorporated into the system optimization. As part of the work package, an energy system model of the Bavarian ChemDelta will be implemented based on industrial data. The model aims to map the heat, electricity, and material flows of the Bavarian ChemDelta in detail. The subsequent energy system optimization includes a scenario-based feasibility study for 100% renewable electricity and material supply. Various transformation scenarios up to 2050 are defined, and the energy system is optimized under the respective conditions. Possible transformation paths of the Bavarian ChemDelta towards H2-based, sustainable production can then be presented and evaluated. Supra-regional, spatially resolved potential studies for renewable energies, as well as biomass and residues, serve as the basis for the energy system optimization. Furthermore, studies are being conducted to establish a circular carbon economy in the ChemDelta.
AP2: Power-to-Methanol und Carbon Capture und Utilization
As part of work package 2, an innovative power-to-methanol container plant is being developed to make a significant contribution to the sustainable chemical industry. The plant is characterized by the coupling of an amine scrubbing process to a residue incineration process in order to effectively capture and use CO2. Methanol is produced by combining the captured CO2 with hydrogen obtained from electrolysis. This methanol serves as a versatile base chemical that can be used in various industrial processes. The process is simulated in Aspen Plus, which formed the basis for the detailed engineering and paved the way for the first plant components to be ordered. This advanced plant will make an important contribution to closing the carbon cycle, representing a milestone towards sustainable energy and chemical production.
AP3: Sustainable Aviation Fuels
In work package 3, a novel biotechnological process for the production of sustainable aviation fuels from biogenic residues is being investigated experimentally and simulatively. Achieving the climate targets regarding the reduction of global CO2 emissions poses a major challenge in aviation, as the electrification of aircrafts is very difficult due to the high energy densities of conventional fuels. Biogenic fuels, which can directly substitute fossil kerosene, are therefore a suitable alternative. In the process under consideration, yeast oil is first formed from straw hydrolysate in a fermentation process, whereby CO2 is produced as a by-product. CO2 is then converted together with hydrogen from electrolysis in a further fermentation process to acetic acid, which can be directly integrated as a reactant for yeast oil fermentation. The yeast oil is thermocatalytically converted into fuels. The experimental investigations of the sub-processes are carried out at TUM by the Chair of Bioprocess Engineering, the Werner Siemens Chair of Synthetic Biotechnology and the Chair of Technical Chemistry II. The Chair of Technical Chemistry II and the Chair of Energy Systems are responsible for the simulative work in Aspen Plus, whereby the focus at CES is on the techno-economic comparison of the biochemical route with alternative paths such as Fischer-Tropsch synthesis or Methanol-to-Jet. The aim is always to model the individual sub-processes as realistically as possible based on experimental data.
AP4: Circular Economy and Waste Utilization
Work package 4 deals with the circular economy and utilization of waste streams in terms of the chemical recycling of complex solid waste fractions (such as chlorine-containing waste, polymers, and sewage sludge). The goal is the closure of the carbon cycle by the exploitation of those heterogeneous fractions. This will be showcased with a container-based pilot plant, supported by process simulations of alternative thermochemical routes.
The two-step process combines pyrolysis and plasma treatment, enabling a flexible system with high carbon efficiency that can cope with a plethora of different feedstocks. The products of the rotary kiln pyrolysis will be transformed into hydrogen-rich synthesis gas employing plasma-assisted entrained flow gasification.
Furthermore, process modelling is applied to examine alternative thermo(chemical) processes for the utilization of sewage sludge in combination with carbon capture in an industrial setting. The objective is to identify a promising process route for the material utilization of sewage sludge in the chemical park of Gendorf.
AP6: CO2 Direct Electrolysis to Green Ethylene
In work package 6, the CO2 direct electrolysis (CODE) to ethylene is to be investigated experimentally and modeled on the basis of experimental data. Ethylene is one of the most important platform chemicals in the chemical industry, which today is almost exclusively obtained from refinery processes. In order to achieve a "green" chemistry, an alternative supply from sustainable process routes is necessary. The direct electrolysis of CO2 and H2 to ethylene offers the advantage of frugality and high selectivity compared to most alternatives and is also more scalable than supply from biogenic sources. In this part of the project, the Chair of Energy Systems is responsible for the process modeling and the techno-economic comparison of the CODE route with alternative routes for the sustainable production of ethylene.
AP7: CO2-negative Production of Hydrogen from Biogas
The research and development in work package 7 focus on an innovative approach that provides both negative and positive control power for the power grid, introduces methane for injection into the gas network, and supplies sustainably produced basic chemicals such as hydrogen and carbon dioxide for the chemical industry. The Chair of Energy Systems and industrial partners are collaborating to advance the technology and implement it as a flexible container solution. The technology is based on the reversible solid oxide cell, which operates at high temperatures and allows for a reversible transition between fuel cell and electrolysis modes in a short time. Additionally, co-electrolysis alongside water electrolysis to produce syngas or methane is also possible. CO2 separation is carried out through a CCU/S facility. The chemical products from the facility can be sold or used as a chemical energy storage. The containerized facility is optimized for enhancing the efficiency, profitability, and climate positivity of biogas plants. The overarching goal is for the entire system to achieve a Technology Readiness Level (TRL) of 7, equivalent to an operational demonstration facility that confirms the functionality of the system and allows for further operational optimizations.
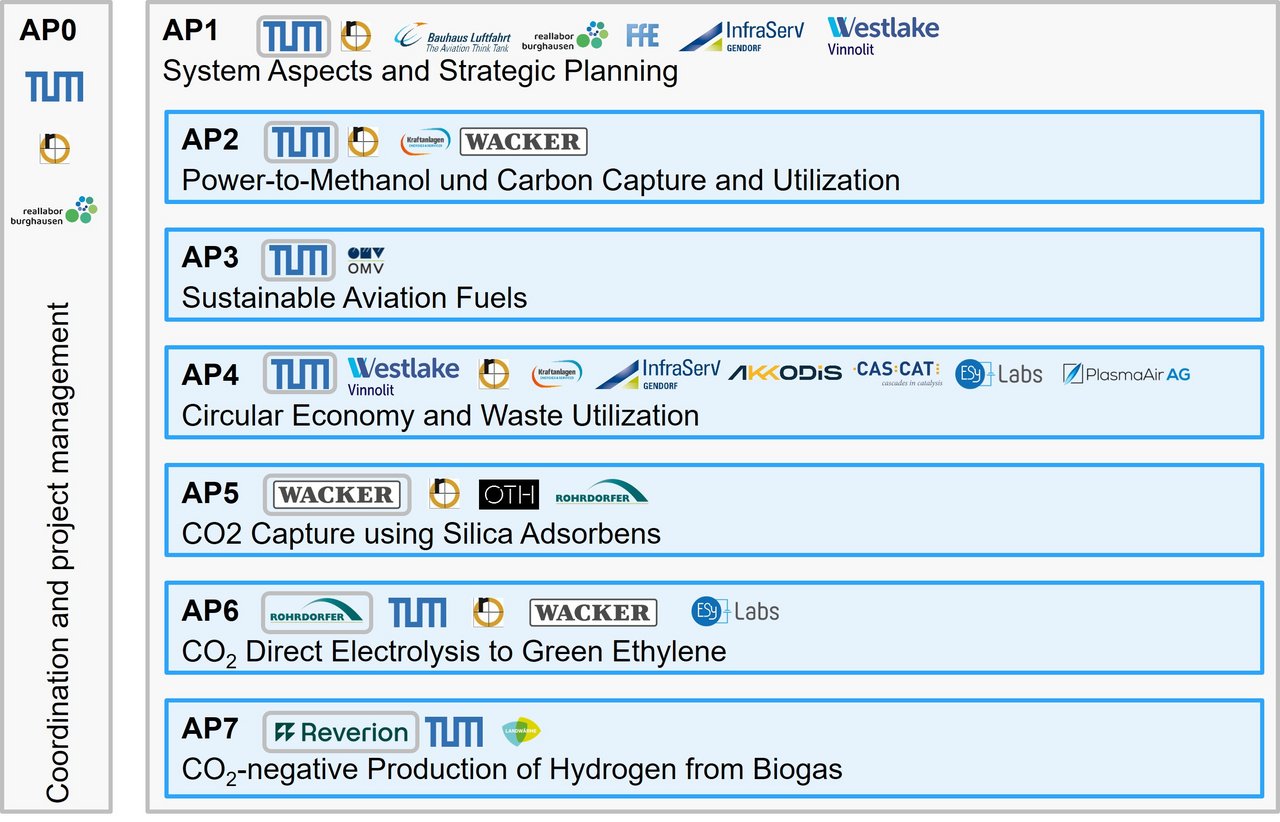
Funding
The H2 Living Laboratory Burghausen project is funded by the Federal Ministry of Education and Research (BMBF) under the funding code 03SF0705B.
Projektpartner
- Technische Hochschule Rosenheim
- Ostbayerische Technische Hochschule Regensburg
- Bauhaus Luftfahrt
- Forschungsstelle für Energiewirtschaft e.V.
- Akkodis Germany Tech Experts GmbH
- Carbon CO2ncepts GmbH
- CASCAT
- ESy-Labs GmbH
- InfraServ GmbH & Co Gendorf KG
- Kraftanlagen Energies & Services GmbH ECM Ingenieur-Unternehmen für Energie- und Umwelttechnik GmbH
- Landwärme GmbH
- OMV Deutschland GmbH (Assoziierter Projektpartner)
- PlasmaAir AG
- Reverion GmbH
- Rohrdorfer / Südbayerisches Portland – Zementwerk Gebr. Wiesböck & Co. GmbH
- Wacker Chemie AG
- Westlake Vinnolit GmbH & Co. KG
